Welcome to visit Jiaozuo xiongshi insulation materials Co. Ltd. Web site!
Contact
Add:The Middle Road South Station area lotus road south city of Jiaozuo Province
Tel:+86 0391-3126228
Fax:+86 0391-3126008
Linkman:Zhangyan Tong(+86 13849503831)
e-mail:xsbwcl@163.com
ProductHome > Product
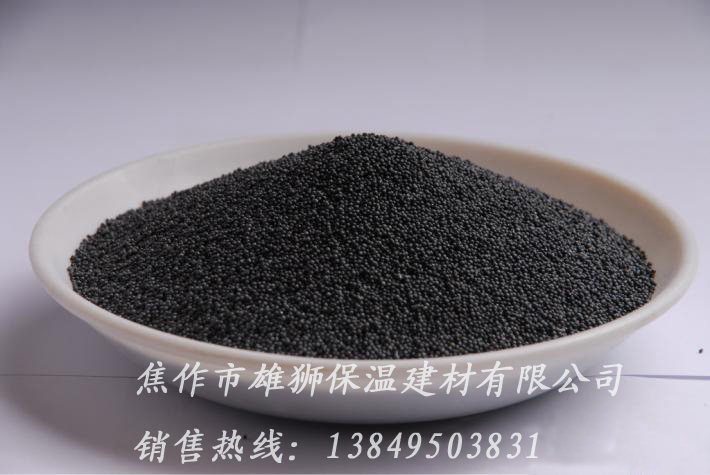
Pearl sand
Detailed description
Also known as the pearl sand fused ceramic, quartz sand is a superior alternative.
Quartz sand has the advantages of wide distribution and low cost, but its disadvantages are also obvious:
First, the expansion coefficient is large, the casting accuracy is low; the two is that the surface of the casting is sticky sand, and the sand is difficult. It is due to the formation of a variety of homogeneous crystals at different temperatures, and the volume changes of the quartz sand, and the size of the quartz sand is 1400 -1700, the casting part (hole, groove, and the hot spots of the site) are sticky, and the ten points are difficult to clean. The above disadvantages in the production of large steel castings is particularly serious. NFS can overcome these shortcomings, thus greatly improving the quality of castings. Pearl sand is made of high quality bauxite as raw material, calcination, electric melting, granulation, sieving technology and made.
The physical and chemical properties of two, pearl sand
Three, pearl sand
. low coefficient of thermal expansion, performance can be comparable with the zircon sand, with its preparation of molding sand, casting does not produce expansion defects. The sand is spherical, good fluidity, easy ramming and ventilation is good. Smooth surface, compact structure, allow the adhesive to can evenly cover. Pearl sand is a neutral materials, acid, alkali binder can use. Back with good regeneration properties, compared to the high price and chromite sand and zircon sand, its price only zirconium English sand, chromite sand 25 - 50%. At the same time, because of the sand is spherical, its surface area is small, so resin dosage can be reduced by up to 30 - 50%, water glass join is equal to or less than 4%; and reduction of bond
Agents arising from the casting defects and improve the rate of finished products of the castings. High refractoriness, easy collapsibility pearl sand of mullite phase is much higher than sintered products, with good fire resistance. High heat conductivity, good stability, not cracking. Application of a wide range of water glass sand, resin sand, fine precision casting and polishing of copper and aluminum parts cleaning
Four, in the production of large castings on the orb
At present, pearl sand widely used in resin sand (furan resin, phenolic resin) and (organic fat, CO 2 hardening water glass sand, resin coated sand. Suitable for all kinds of metal castings, such as: carbon steel, alloy steel (Gao Menggang, high chromium cast iron), cast iron, cast copper, etc..
Five, pearl sand in large complex on the casting
Yulin Diesel Engine Factory by pearl sand production diesel engine water suite, maintain the original with characteristics of sand, to overcome the original sand expansion coefficient, binder, volume big and so on shortcomings and reduce the resin amount, improve the rate of finished products.
Six, the pearl sand in large steelcastings
Fujian Sanming triple all use pearl sand, adding water glass by 3.2%, all of the core, the shape not brush paint, use found that smooth casting surface, no sand sticking, and low energy consumption. Sand recycling equipment is quite simple. Luoyang Luobei steel production 13 tons of cement production equipment - rotary kiln supporting roller. The core (phi 90mm, long 800mm) with 30-40 to pearl sand as raw sand, adding 3.5% water glass, CO2 hardening. Other parts with silica sand as raw sand, do not change the original method of use. When cleaning, core surface of shell is only 0.2mm thick black glaze surface arranged in an orderly manner, not is sintered, and easy to be cleared away; in other used parts of silica sand, shell surface with 3 - 8mm thick sintering black glaze layer. Luoyang Luobei steel mills, Ruyang Xingrong machinery factory, Shandong Hengcheng casting plant, dozens of manufacturers, at 30 - 40 mesh sand pearl sand in and join the 140 - 320 to fine sand 20% - 30%. The results showed that the same no sand sticking, and have sufficient ventilation, is easy to clean. In order to reduce the production cost, some steel mills have adopted the method of local single surface sand, and the effect of non stick sand is also played. After long-term exploration and casting factory, summed up: the thickness of the sand surface to 10 - 20 mm (Chung tight thickness); the shape is complex, the thick part, the corner, an appropriate increase in the thickness and sand back still use ordinary quartz sand. Effect of the sand and quartz sand mixed use, proportion is changed according to the change of size of castings, steel, also reached the no sand sticking and easy collapsibility.
The application prospects of the seven, pearl sand on auto parts
For a long time, automobile industry ranked foundry industry's largest market, in recent years the development of China's automobile industry is constantly pulling foundry industry entered a new period of development, and the rapid development at the same time, also contributed to the foundry industry market's rapid expansion, and gives the broad prospects for development. China's auto parts casting market prospects, the total output of our country is expected to reach 15000000 in 2015, the price of 120000 yuan price calculation, the whole car accessories generally around 80000 yuan, the new car parts foundry market size in 2015 will reach 1200000000000 yuan.
Eight, the pearl sand application conclusion
Pearl sand is a kind of non quartz type artificial sand, applicable to all kinds of casting; such as V method VRH, lost foam, fusion model and general sand (clay sand, water glass + CO 2 hardening), resin sand; for in a variety of adhesives, all kinds of metal materials of casting production, not only can greatly improve quality of castings, and sand cleaning easy, sand preparation process is simple and convenient (large steel plant in single piece and small batch local sand, a small amount of sand artificial mixed system can), for most of the casting can save coating, especially suitable for making high - quality of castings. Note: in the use of water glass CO 2 hardening sand, dry core, type, not to drying kiln (such as drying must control the heating rate). With the casting industry development and the social environmental protection requirements, partial and full use of pearl sand manufacturers will be more and more, it has is known as environmentally friendly green BEADS) casting material, has good popularization and application prospect.
Pearl sand effectively solve the castings of high cost and poor quality of casting problems disappear casting enterprises in recent years by the influence of many factors, resulting in production of qualified rate of casting finished products is not high, the casting production costs are high, the defective rate high, low quality characteristics has become placed in the lost foam casting enterprise three seat Ju Shan, how to solve these problems, an early riser casting products price become the domestic foundry enterprise is one of the most important tasks. As is known to all, the selection of sand in the casting is link is of vital importance to the whole process, once the sand not appropriate to select will affect the entire global, so the lost foam casting enterprises should be more effort on the choice of sand. According to relevant data shows, at present domestic most casting enterprise has in the sand choice is improved, to abandon the traditional low price of quartz sand or magnesium olivine sand, the new pearl sand to improve casting problems. The new type of sand is the college and enterprise joint product and the refractoriness, liquidity good and highly breathable advantages, in a certain extent, to solve the defects in the casting production, and thus have international casting industry wide attention and become the new darling of lost foam casting. Enterprise cost of castings in lost foam casting, defective rate, quality problems have been effectively alleviated, also pearl sand has also been fond of many enterprises.
Next:Asbestos rope